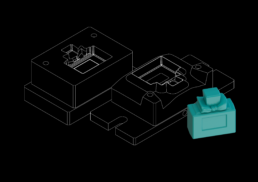
1. Shape challenge – Solid soap dispenser
Designer, artistic or carved shapes? It’s easy if you know how to do it. A detailed feasibility study and the development of the product design are always crucial and make the difference between success and failure. Our experience in defining the details and designing the mould, including the special suction cup, has been the key factor for the excellent results we have achieved.
2. Triple level challenge – soap with central hole
The shape posed a challenge at three different levels: highly irregular edges, the central hole and the soap formula. Developing the design was therefore a tricky process for automated production, but thanks to our experience and our team’s problem solving skills we proved once again that we were able to rise to the challenge.
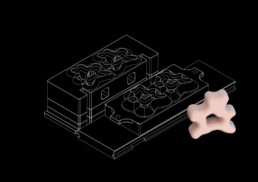
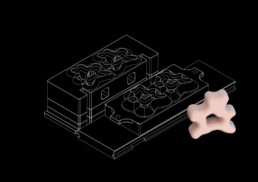
2. Triple level challenge – soap with central hole
The shape posed a challenge at three different levels: highly irregular edges, the central hole and the soap formula. Developing the design was therefore a tricky process for automated production, but thanks to our experience and our team’s problem solving skills we proved once again that we were able to rise to the challenge.
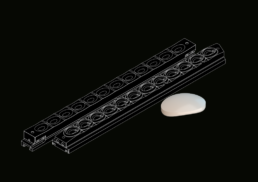
3. Cavities challenge – 12 cavity mould
Driven by the demand for high productivity, we have successfully produced moulds with up to 16 cavities, a process involving very different challenges from those we faced in previous cases. In this case, priority had to be given to the choice of materials with high thermal conductivity, the efficiency of the cooling system and the non-stick treatment of the mould, without losing sight of the high quality standard required for the soap itself.
Would you like to know more?
Request the company profile from